Det franske solenergiinstituttet INES har utviklet nye PV-moduler med termoplast og naturlige fibre hentet i Europa, som lin og basalt.Forskerne tar sikte på å redusere miljøfotavtrykket og vekten til solcellepaneler, samtidig som de forbedrer resirkuleringen.
Et resirkulert glasspanel foran og en linkompositt på baksiden
Bilde: GD
Fra pv-magasinet Frankrike
Forskere ved Frankrikes nasjonale solenergiinstitutt (INES) – en avdeling av den franske kommisjonen for alternativ energi og atomenergi (CEA) – utvikler solcellemoduler med nye biobaserte materialer foran og bak.
"Ettersom karbonfotavtrykket og livssyklusanalysen nå har blitt essensielle kriterier i valget av solcellepaneler, vil innkjøp av materialer bli et avgjørende element i Europa i løpet av de neste årene," sa Anis Fouini, direktør for CEA-INES , i et intervju med pv-magasinet Frankrike.
Aude Derrier, forskningsprosjektets koordinator, sa at kollegene hennes har sett på de forskjellige materialene som allerede eksisterer, for å finne en som kan tillate modulprodusenter å produsere paneler som forbedrer ytelsen, holdbarheten og kostnadene, samtidig som de reduserer miljøpåvirkningen.Den første demonstratoren består av heterojunction (HTJ) solceller integrert i et komposittmateriale.
"Forsiden er laget av en glassfiberfylt polymer, som gir gjennomsiktighet," sa Derrier."Baksiden er laget av kompositt basert på termoplast der en veving av to fibre, lin og basalt, er integrert, som vil gi mekanisk styrke, men også bedre motstand mot fuktighet."
Linen er hentet fra Nord-Frankrike, hvor hele det industrielle økosystemet allerede er til stede.Basalten er hentet andre steder i Europa og er vevd av en industriell partner av INES.Dette reduserte karbonavtrykket med 75 gram CO2 per watt, sammenlignet med en referansemodul med samme effekt.Vekten ble også optimalisert og er mindre enn 5 kilo per kvadratmeter.
"Denne modulen er rettet mot PV- og bygningsintegrasjon på taket," sa Derrier.«Fordelen er at den er naturlig svart i fargen, uten behov for et baksideark.Når det gjelder resirkulering, takket være termoplast, som kan omsmeltes, er separasjonen av lagene også teknisk enklere.»
Modulen kan lages uten å tilpasse aktuelle prosesser.Derrier sa ideen er å overføre teknologien til produsenter, uten ytterligere investeringer.
"Det eneste imperativet er å ha frysere for å lagre materialet og ikke starte harpiks-tverrbindingsprosessen, men de fleste produsenter i dag bruker prepreg og er allerede utstyrt for dette," sa hun.
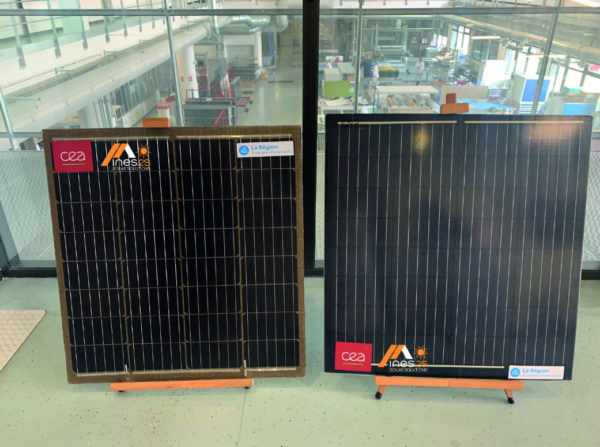
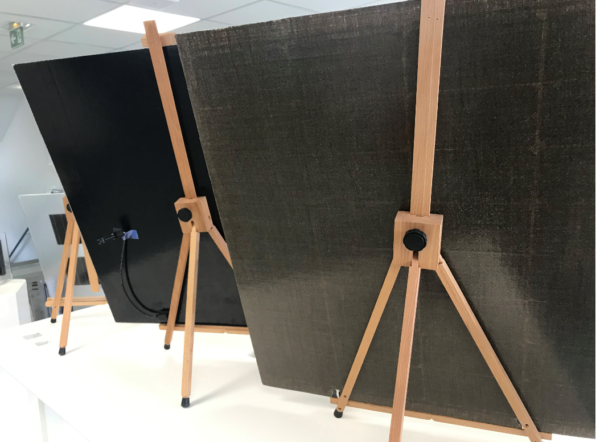
"Vi jobbet med glassets andre levetid og utviklet en modul som består av gjenbrukt 2,8 mm glass som kommer fra en gammel modul," sa Derrier."Vi har også brukt en termoplastisk innkapsling som ikke krever tverrbinding, som derfor vil være lett å resirkulere, og en termoplastisk kompositt med linfiber for motstand."
Den basaltfrie baksiden av modulen har en naturlig linfarge, som kan være estetisk interessant for arkitekter med tanke på for eksempel fasadeintegrasjon.I tillegg viste INES-beregningsverktøyet en reduksjon på 10 % i karbonavtrykket.
"Det er nå viktig å stille spørsmål ved de fotovoltaiske forsyningskjedene," sa Jouini.«Med hjelp fra Rhône-Alpes-regionen innenfor rammen av den internasjonale utviklingsplanen, gikk vi derfor på jakt etter aktører utenfor solenergisektoren for å finne ny termoplast og nye fibre.Vi tenkte også på den nåværende lamineringsprosessen, som er veldig energikrevende.»
Mellom trykksettingen, pressingen og avkjølingsfasen varer lamineringen vanligvis mellom 30 og 35 minutter, med en driftstemperatur på rundt 150 C til 160 C.
"Men for moduler som i økende grad inneholder øko-designede materialer, er det nødvendig å transformere termoplast ved rundt 200 C til 250 C, vel vitende om at HTJ-teknologi er følsom for varme og ikke må overstige 200 C," sa Derrier.
Forskningsinstituttet slår seg sammen med den Frankrike-baserte induksjonstermokompresjonsspesialisten Roctool, for å redusere syklustider og lage former i henhold til kundenes behov.Sammen har de utviklet en modul med en bakside laget av termoplastkompositt av polypropylentype, som resirkulerte karbonfibre er integrert i.Forsiden er laget av termoplast og glassfiber.
"Roctools induksjonstermokompresjonsprosess gjør det mulig å varme opp de to front- og bakplatene raskt, uten å måtte nå 200 C i kjernen av HTJ-cellene," sa Derrier.
Selskapet hevder investeringen er lavere og prosessen kan oppnå en syklustid på bare noen få minutter, samtidig som den bruker mindre energi.Teknologien er rettet mot komposittprodusenter, for å gi dem muligheten til å produsere deler i ulike former og størrelser, samtidig som de integrerer lettere og mer holdbare materialer.
Innleggstid: 24. juni 2022